You can only gain access to certain items and special pricing if you have logged in. Login Now.
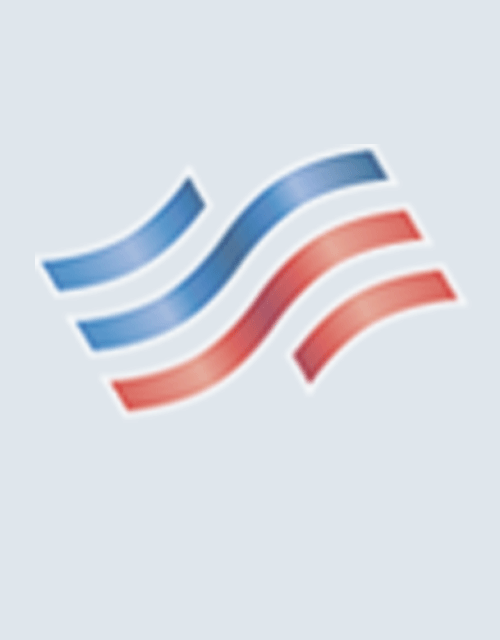
AM-97-32 FCC UNIT OPTIMIZATION USING THE MAGNACAT PROCESS
Terry L. Goolsby; Ashland Petroleum Company Ashland, Kentucky
Format:
Electronic (digital download/no shipping)
Associate Member, International Member, Petrochemical Member, Refining Member -
$0.00
Government, NonMember -
$35.00
Description:
The refining industry has experienced numerous changes in markets and refining operations. Refiners are looking hard at cutting costs, improving FCC operating efficiency and for processes which improve refining margins with the least amount of capital investment. Fluid catalytic cracking (FCC) in particular has a significant bottom line impact on both refining revenue generation and cost. FCC costs include fresh catalyst purchases as well as spent catalyst disposal which can be significant at times. Both of these can be offset to a degree by utilization of,a5new process c$lsed MagnaCat@. A series of previously published technical articles and patents - describes this technique for using high field strength permanent magnets to continuously remove the older, higher metals laden, less active fluid cracking catalyst from the equilibrium FCC inventory by dry magnetic separation techniques to produce a catalyst with lower metals and higher activity and selectivity. The first commercial application of this .technology has been successfully operating since April of 1996 at Ashland Petroleum’s Canton, Ohio refinery. This paper describes the implementation of the MagnaCatB Process at the Canton refinery for upgrading FCC catalyst on a continuous basis. Since start-up, substantial improvements have been observed in the conversion level and product profile of the Canton FCC unit yielding significant economic benefits. The final section of the paper describes the design of the MagnaCatB process unit developed for commercial licensing.
Product Details:
Product ID: | AM-97-32 |
---|---|
Publication Year: | 1997 |