You can only gain access to certain items and special pricing if you have logged in. Login Now.
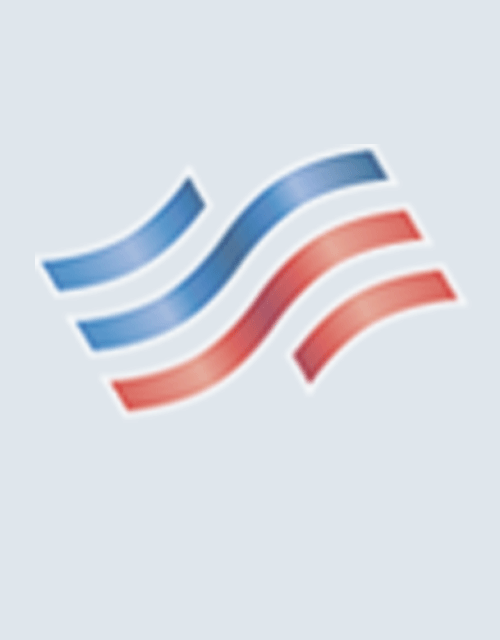
AM-00-31 COMMERCIAL EXPERIENCE WITH IMPROVED HYDROCRACKING CATALYSTS
Dan M. Torchia, Akzo Nobel Catalysts LLC
Format:
Electronic (digital download/no shipping)
Associate Member, International Member, Petrochemical Member, Refining Member - $0.00
Government, NonMember - $25.00
Description:
The hydrocracker should be recognized as the most technically complex and challenging of process units at a refinery. It usually involves multiple reactors, each with multiple beds, in series and/or parallel, resulting in a feed and product specific configuration that is probably unique in the world. Unlike many other major refinery process units, the hydrocracker must meet catalyst cycle requirements and is relatively unforgiving. Hydrocrackers do, however, generally have amongst the highest refinery base margins and usually the highest incremental margins. In addition, since the unit has a high operating cost, there is always an incentive to maximize throughput to reduce per-barrel cost. Hydrocrackers are capable of processing a wide variety of feedstocks and of producing a variety of very high quality, environmentally sound products. These parameters can be changed mid-cycle to meet market opportunities. Because of their tremendous flexibility and added value, these units are generally operated well over design conditions. This trend will continue due to environmental pressure and legislated clean fuel issues. As a result, proper catalyst choice is more important now than ever before and the key to proper unit utilization and maximum profit. As refiners are pressured to operate at higher efficiency levels and at lower cost, hydrocracker performance becomes even more significant and highly visible. Since the hydrocracker often dictates area turnaround schedules, achieving longer runs will have a positive impact on other refinery units and the savings will multiply. Equally important is utilization of the run and completion of a cycle as planned, without inefficient, last minute, high cost cycle extensions. Since hydrocrackers produce very low or no-sulfur products, they play an increasing role with clean fuels components and operating reliability will have a significant impact on the ability to blend and sell product. For these reasons, careful consideration should be given to proper evaluation of unit objectives and catalyst selection to achieve those objectives. This paper will describe the commercial experience with two of Akzo Nobel’s latest hydrocracking catalysts, Ketjen cracking KC-2710 and Ketjenfine KF-1015MD. KC-2710 is a maximum naphtha/kero selective catalyst that produces a high yield of premium quality products with remarkable operating and yield stability. KF-1015MD is a maximum distillate catalyst designed to produce very high yields of premium quality diesel and kerosene. These two catalysts have commercially demonstrated exceptional performance to produce very selective, premium quality products and longer cycles over the full range of products from gasoline to diesel. Coupled with Akzo Nobel/Nippon Ketjen’s high activity deep HDN/HDS pretreat catalysts such as KF846 and STARS technology KF-848, unmatched performance can be realized to achieve longer operating cycles with higher product yields and qualities.
Product Details:
Product ID: | AM-00-31 |
---|---|
Publication Year: | 2000 |