You can only gain access to certain items and special pricing if you have logged in. Login Now.
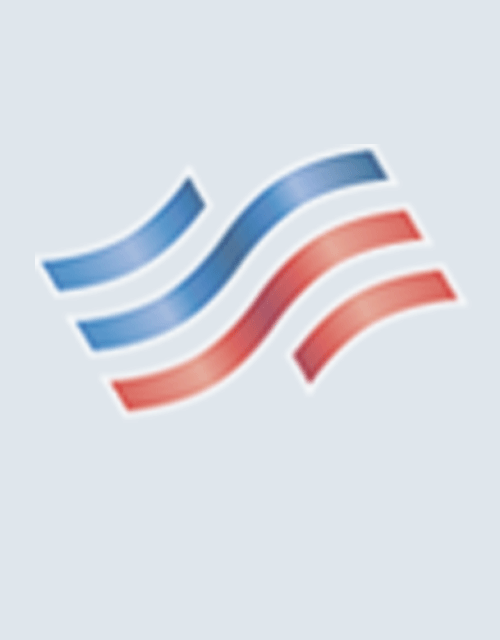
AM-13-42 Reactor Effluent Air Cooler (REAC): Safety Through Design
Eric Lin, Peter Risse, Chevron
Format:
Digital
Associate Member, International Member, Petrochemical Member, Refining Member - $0.00
Government, NonMember - $35.00
Description:
In hydroprocessing units, the reactor effluent cooler (REAC) is one of the most vital pieces of equipment and any hindrance to its smooth operation immediately impacts the whole high-pressure loop. Older REAC designs used carbon steel (CS) but these required low concentrations of ammonium bisulfide and/or polysulfide sulfide injection together with frequent and thorough inspections. As feeds in most heavy oil hydroprocessing service have become more laden with sulfur and nitrogen, the concentrations of ammonium bisulfide with economic levels of water injection, have risen to a point where CS tubes have routinely been substituted by alloy tubing. Duplex 2205 and Alloy 825 are used with the former being very popular because it is relatively less expensive. Initially there were several problems associated with Duplex 2205 that were a result of poor fabrication techniques including rapid cooling rate associated with thick header boxes which could result in high Ferrite and thus poor corrosion resistance; welding of thick tubes to tubesheets with joint leaks, lack of control of welding resulting in high hardness and thus susceptibility to Sulfide Stress Cracking. Many of the initial problems associated with Duplex 2205 seem to have been overcome. Surrounding the REAC however, problems persist primarily because of lack of attention to detail and not adhering to licensor specifications. In this paper we will illustrate real problems around the REAC from recent projects and the remedies that were recommended.
Product Details:
Product ID: | AM-13-42 |
---|---|
Publication Year: | 2013 |