You can only gain access to certain items and special pricing if you have logged in. Login Now.
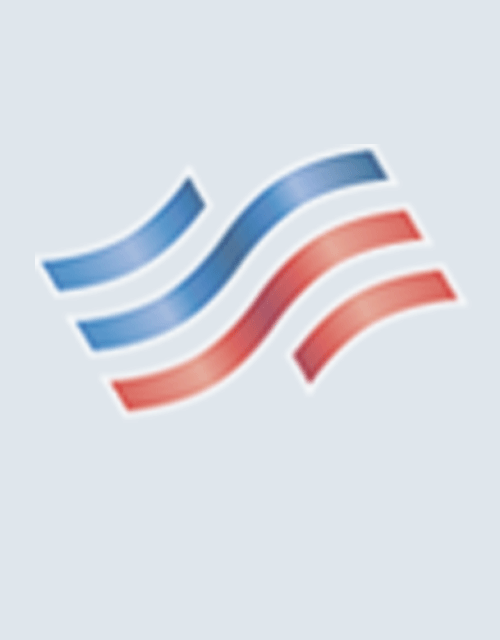
AM-17-33 Minimum Disruption Plan (MDP) to Asset Life Extension
Odette Eng Advisian/Worley Parsons Monrovia, CA
Format:
Electronic (digital download/no shipping)
Associate Member, International Member, Petrochemical Member, Refining Member - $0.00
Government, NonMember - $35.00
Description:
Many industrial complexes such as refineries, upgraders, and petrochemical complexes have been in operation for numerous decades. But with their advanced ages and high utilization rates, they require ever-rising inspection, maintenance, and repair costs to be able to operate reliably. Management of these assets is now confronted with difficult decisions: continue to pay for these rising maintenance and repair costs as equipment approaches the end of their useful life, or retire and replace these specific equipment. These decisions need to be made in a timely manner before certain pieces of equipment and the supporting infrastructure become a liability. To get to the right answers, management and reliability and maintenance organizations need to collect and evaluate a great deal of assessment data from the overall plant to determine the health of the assets. This data should be collated from the equipment perspective to the supporting systems such as civil/structural, electrical, I&C, etc. However, for planning purposes, management of these assets would want to know answers to the following questions: 1. How long should they plan for the equipment replacement window? 2. In planning for construction logistics, what is a rough order of magnitude of how many pieces of equipment should be replaced for end of life? 3. What is the order of magnitude of capital expenditures required? What would be the long range capital outlay to spread out this capex without putting the plant at risk? 4. How would the life extension program affect the normal operations of the running plant? 5. How many activities can be shifted away from the major turn-around windows to minimize disruptions to normally planned activities and costs? 6. What are the implementation steps? In this presentation, Advisian/WorleyParsons will share how we brought clarity to this aforementioned multi-faced issue. Through an engagement with a major plant, we brought answers and clarity to the owner, utilizing the skillsets of a cross-functional team as well as our long established experience to arrive at a bird’s eye view and identified opportunities to improve cash flow.
Product Details:
Product ID: | AM-17-33 |
---|---|
Publication Year: | 2017 |