You can only gain access to certain items and special pricing if you have logged in. Login Now.
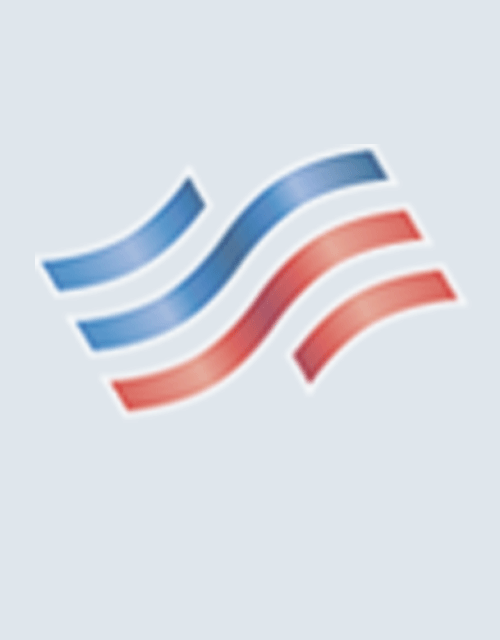
AM-97-58 MINIMUM INVESTMENT REVAMPS PROCESS DESIGN AND ACHIEVING ATTRACTIVE ECONOMICS
Scott W. Golden; Process Consulting Services Inc. Houston, Texas
Format:
Electronic (digital download/no shipping)
Associate Member, International Member, Petrochemical Member, Refining Member - $0.00
Government, NonMember - $35.00
Description:
Revamping refinery units can improve economics with minimum capital investment. However, often they fail to meet their stated objectives”‘. Minimum investment revamps must eliminate existing unit bottlenecks while pushing the unit to its next major investment cost bottleneck. By definition, minimum-cost revamps push the existing equipment to maximum performance without unnecessary investment. Conventional project management focuses resources on organizational issues and efficiencies to lower project cost. Minimum investment revamps focus resources on measuring the existing unit equipment performance, conceptual process design, and detail equipment design”‘. Effective process design will minimize investment cost, not conventional project hierarchical groups performing multiple work activities’. Reliable revamps address the following: : Accurately measure unit performance: specific equipment bottlenecks : Conceptual process design: cost-effective bottleneck elimination : Specific equipment bottlenecks: reliable operating revamps All phases of a revamp must be addressed to meet economic and-reliability objectives. Minimizing capital investment first requires identifying the equipment bottlenecks that cause unit throughput, product quality, or reliability problems. Unit bottlenecks generally show-up as symptoms such as low heater inlet temperature, high vacuum column pressure, or black FCC feedstock. Often, conclusions are made as to the cause of operating problems based on inaccurate or no hard data, even if there are several possibilities. For instance, on a crude unit, low heater inlet temperature is commonly assumed to be caused by inadequate heat exchanger surface area. Therefore, a revamp will add more crude preheat exchanger surface area to increase crude oil preheat. Increased surface area may not be the lowest cost and most reliable revamp to increase crude oil preheat. Revamps require a thorough understanding of the specific system or equipment bottlenecks. Identifying the specific equipment bottlenecks that create the symptom requires accurate field measured data. Once the specific bottleneck is identified, it can be circumvented by process flow or equipment modifications. Whether the process or equipment revamp cost is $l,OOO,OOOor $2O,OOO,OOOth,e cost is minimized by maximum utilization of existing equipment and making judicious equipment modifications. Ultimately revamps must meet their stated objectives over a 3-5 year run length. A revamp investment must be reliable.
Product Details:
Product ID: | AM-97-58 |
---|---|
Publication Year: | 1997 |