You can only gain access to certain items and special pricing if you have logged in. Login Now.
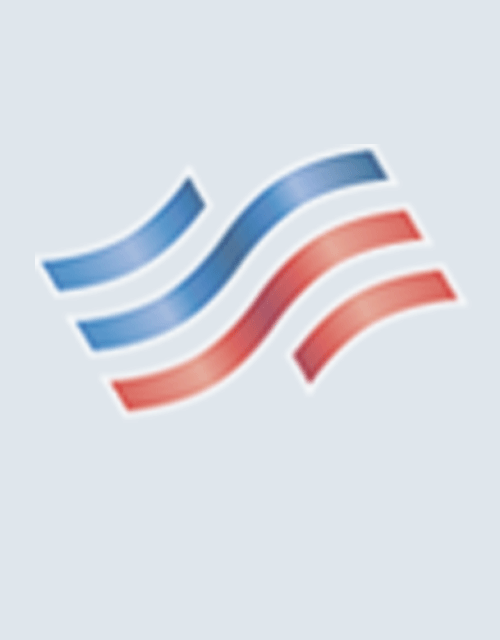
ENV-05-197 Extension of NOx Correlation to Ethylene Cracking Furnaces
Robert Kunz, RGK Environmental Consulting, L.L.C.
Format:
Digital
Associate Member, International Member, Petrochemical Member, Refining Member, Special/Temporary Member - $0.00
Government, NonMember - $25.00
Description:
Allowable emission limits for nitrogen oxides (NOx) are becoming increasingly more stringent as regulatory agencies carry out their mandate to control excessive concentrations of ground-level ozone. The ozone is formed in the atmosphere by the sunlight-induced reaction of NOx with certain hydrocarbons. This rulemaking affects combustion sources in the petroleum refining and petrochemical industries, including the many ethylene plants located along the U.S. Gulf Coast in Texas and Louisiana. It is understandable that operators there would prefer to minimize the additional cost and complexity to achieve compliance by means of burner modifications in the furnace, rather than through post-combustion controls such as selective catalytic reduction (SCR). However, there is a trade-off between flame stability and decreased burner NOx. Although cases require long convergence times, computational fluid dynamics (CFD) has been employed successfully to model flame patterns, furnace temperatures, and the like. Nonetheless, experts agree that CFD modeling does a poor job in predicting burner NOx. Likewise, burner testing in a pilot furnace without the full array of burner-to-burner interactions often produces low estimates for NOx when compared to a full-scale furnace. This suggests trying an empirical approach to predict NOx as a complement to CFD. To that end, this paper presents a new correlation of NOx emissions from ethylene cracking furnaces. It is derived from an established NOx correlation for commercial steam-methane reformer (SMR) furnaces, recognizing the differences in fuels and furnace conditions between the two processes. It uses adiabatic flame temperature (AFT), excess furnace oxygen (O2), and furnace temperatures. Calculations can be accomplished rapidly and allow one to compute accurate values of NOx, assess effects of changing input variables, and explain experimental observations. Results are compared with available NOx data reported for commercial ethylene furnaces spanning a wide range of conditions.
Product Details:
Product ID: | ENV-05-197 |
---|---|
Publication Year: | 2005 |