You can only gain access to certain items and special pricing if you have logged in. Login Now.
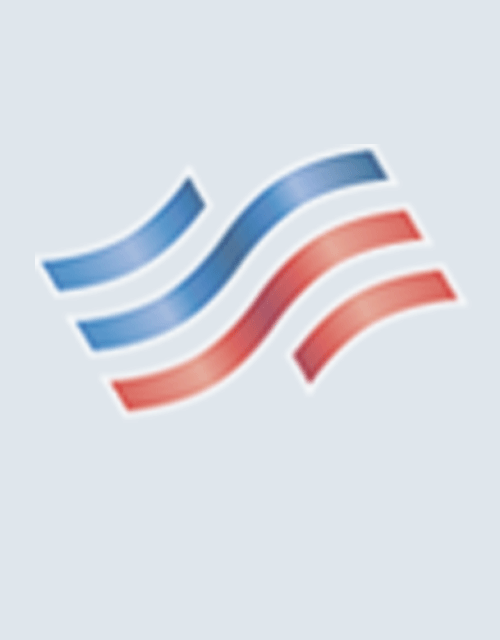
PD-11-01 Controlling Hydrocracker Temperature Excursions
Gregory W. Hampton Advanced Process Control Engineer CITGO Petroleum Corporation Lake Charles, LA Paul R. Robinson Senior Engineer, Hydrocracking Technical Service Criterion Catalysts & Technologies LP Houston, TX
Format:
Electronic (digital download/no shipping)
Associate Member, International Member, Petrochemical Member, Refining Member - $0.00
Government, NonMember - $35.00
Description:
The hydrocracker at the CITGO Lake Charles Manufacturing Complex in Louisiana upgrades gas oils and cycle oils to naphtha, jet fuel and diesel fuel in the presence of hydrogen. The unit has eight fixed catalyst beds in series – three beds in a pretreat reactor and five beds in two cracking reactors. The inlet temperature of the first cracking bed is controlled with a hydrogen heater and a recycle oil heater. The remaining bed inlet temperatures are controlled with hydrogen quench. Overall, hydrocracking reactions are highly exothermic, so design and operation revolve around heat control. A high temperature excursion can lead to loss of hydrocarbon containment, catalyst deactivation and lost production. Excursions can be avoided with hydrogen quench, reduced heater firing and reduced preheat. The last resort is unit depressurization, which is very disruptive to operations. Conventional quench control strategies have a bed inlet temperature controller for each bed. Here each cracking bed has a bed inlet temperature controller with overrides for three constraints: peak temperature, quench demand and output negative rate of change. The quench demand of each bed is calculated based on the peak bed temperature and the bed rate of change in °F/min. The quench demand constraint provides early detection of a temperature excursion with the appropriate preemptive action.
Product Details:
Product ID: | PD-11-01 |
---|---|
Publication Year: | 2011 |