You can only gain access to certain items and special pricing if you have logged in. Login Now.
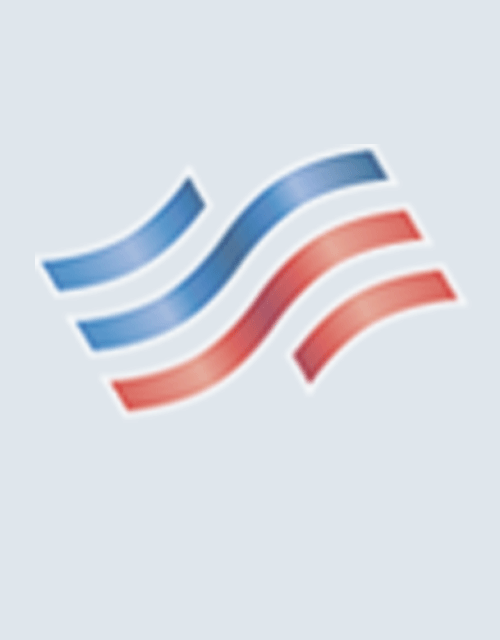
Recent Changes In Refinery Materials And Corrosion – A Major Impact On Reliability
C.A. Shargay, A.R. Smith, Fluor Corporation
Format:
Digital
Associate Member, International Member, Petrochemical Member, Refining Member - $0.00
Government, NonMember - $25.00
Description:
One of the new buzz-word phrases being widely used at the Materials Engineers’ conferences these days is “Process Creep”. This refers to the trend for units to gradually increase in temperature, flow rates, contaminant levels etc., with no single change being large enough to trigger a full review, but with the cumulative effect being significant. This has been one “source” of changes affecting refinery materials, corrosion and reliability, and it is one of the more subtle ones. Other sources of these changes can be categorized as: ? feed changes (such as bringing in opportunity crudes), ? product spec changes often from stricter government regulations, ? increased understanding of the corrosion mechanisms and solutions, ? new materials or new knowledge on where they should and shouldn’t be used, and ? industry trends of process improvements to specific units. Examples of the latter have been the trend to add Hot High Pressure Separators (HHPS) to new or revamped hydroprocessing units, or the trend of increasing temperatures in FCC reactors and regenerators. This paper will focus on the recent changes in each category. This paper will use the term “Materials Engineer”, but this person may have different titles at different companies or sites. Other titles can include Corrosion Engineer, Reliability Engineer, Chief Inspector, etc. In some plants, the duties are assigned to one or more Process Engineers. The typical responsibilities can include: - selecting materials for new or replacement piping and equipment, - recommending special fabrication steps needed for process reasons, such as postweld heat treatment, - conducting failure analyses of cracked or corroded components, - recommending special inspection programs, - reviewing proposed process changes for acceptability with the existing materials, - recommending or reviewing chemical additive programs (e.g. inhibitors, water washes, etc.) - reviewing utility treatment programs, etc.
Product Details:
Product ID: | AM-03-70 |
---|---|
Publication Year: | 2003 |